|
Application Flexibility
Flow Well Design
• Wave configuration is a critical factor in reflow desoldering and resoldering operations.
• Flow Wells determine the solder wave, which matches the component lead pattern.
• The solder flow can be accurately directed away from adjacent components to limit
• heat exposure to sensitive areas of the assembly.
Application Specific Tooling
• Successful reflow soldering and rework is related to the flow well design.
Send your board or layout to Air-Vac for a quick response to simplify your
process and improve your productivity.
• Customer support is critical for successful solutions. Air-Vac takes responsibility for
• the process by receiving the assembly, discussing the application, quoting the flow
• well, and developing a proven process prior to shipment.
Standard Flow Wells and Cleaning Hoods
• Air-Vac maintains an assortment of standard flow wells and cleaning hoods.
• We have 23 standard size titanium Flow Wells.
• We have 23 standard size Cleaning Hoods (in conjunction with the APS option).
• The corresponding air cleaning hood positions the component over the flow well.
• After component removal, the hood directs low pressure air against the lead pattern,
• forcing molten solder to drop from the holes into the empty flow well.
• Visit Flow Well web page >
Custom Designed Flow Wells and Cleaning Hoods
• Air-Vac specializes in custom specific tooling for complex boards.
• Visit Flow Well web page > |
|
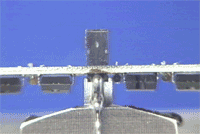
Solder flow is directed away from adjacent components.
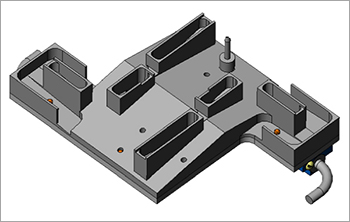
Custom Flow Well example, engineered for any component configuration.
|
|